Supply Chain Issues
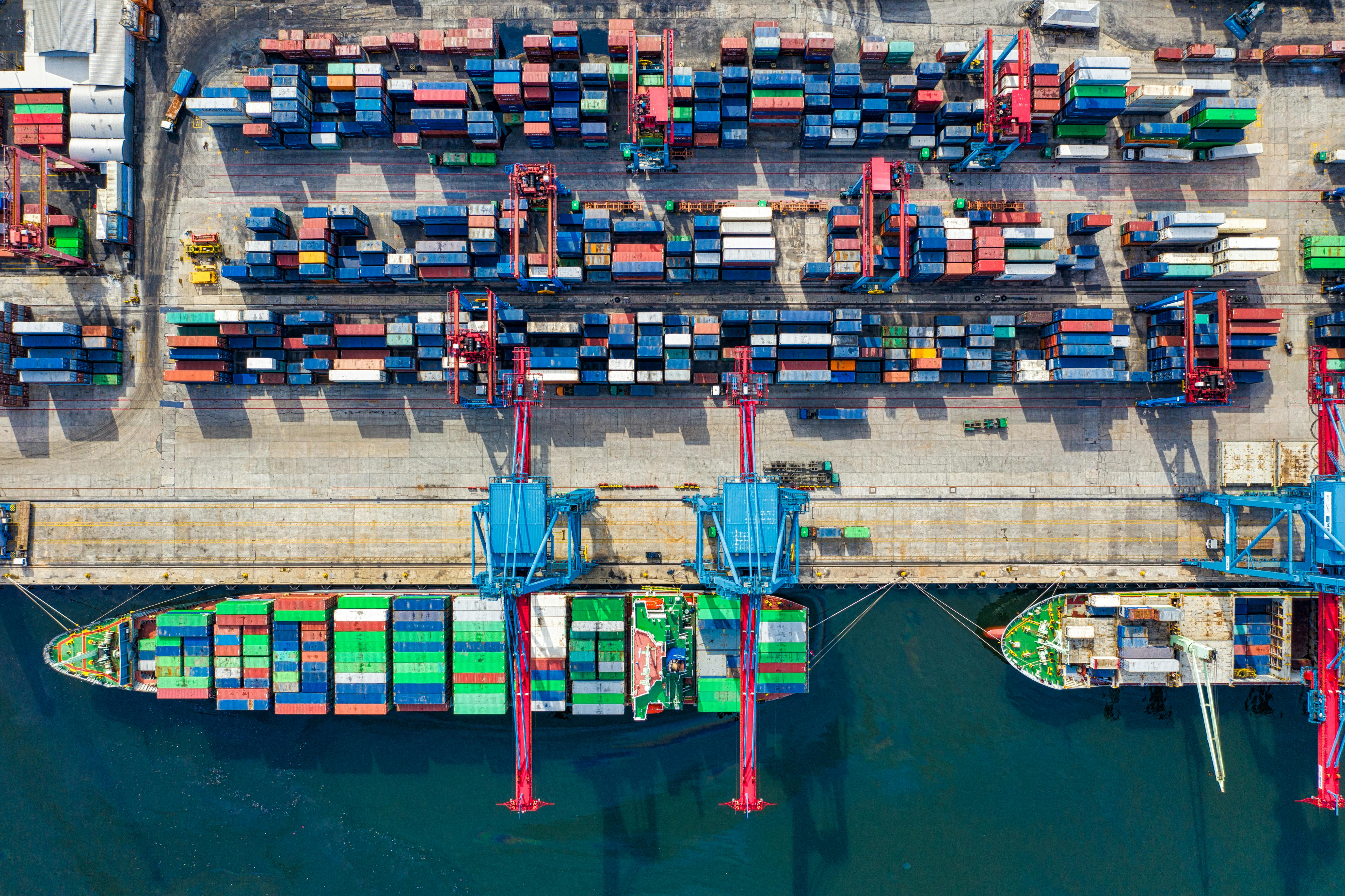
Image Source: Pexels
Supply chain management is a key function for almost every organization. When an organization has a well-oiled supply chain, it can reduce costs, meet customer demand, and avoid stock-outs. However, even the best companies can experience problems with their supply chain. Unforeseen issues may arise that cause supply chain disruptions, lead to stock-outs or leave shelves empty in stores. Here are some of the most common supply chain issues.
End-of-year inventory scramble
Many retailers experience an inventory scramble at the end of the year. They find themselves facing a combination of customers who want to purchase gift cards and items that are already out of stock. This puts pressure on the supply chain to increase inventory and/or put in rush orders with suppliers. To avoid this inventory scramble, retailers can plan ahead of time by noting the common gift card items and stocking enough of those items throughout the year.
Excessive inventory
If too much inventory is flowing through the supply chain, there may be a problem with demand forecasting. Having too much inventory can lead to excess inventory. Inventory levels should be closely monitored. If the inventory levels are too high, some items may be out of stock at the store level. If this is the case, the company should look into why the inventory levels are too high. One possible cause is that the company is not putting enough emphasis on forecasting. Forecasting is crucial to supply chain management. It’s important to not only predict how much of each item will be sold but also how much will be returned and how much will be lost due to breakage.
Incorrect product assortment
If products are incorrectly stocked or incorrectly priced, this will throw off the system. Product assortment is a top issue when stocking shelves or placing orders. If products are incorrectly stocked at the store level, customers will not be able to find what they are looking for. At that point, they may choose to shop at another store that has the products in stock. This is also a problem on the ordering side. If products are not stocked at the store level, it is likely that they weren’t ordered when they were ordered. Incorrect product assortment can adversely affect the bottom line.
Poor stock rotation and shelf calibration
Many supply chain issues can be traced to poor stock rotation. If products are not being rotated from the front of the store to the back of the store, and other products are not being rotated in their place, this can lead to expired goods on the shelf. It can also lead to incorrectly priced items. If something is mispriced, customers may be purchasing items that are not correct for their needs. Poor stock rotation can also lead to incorrect product assortment.
Defective or damaged goods in the supply chain
Retailers want to receive products that are in good condition. However, sometimes products arrive at the store with defects or they arrive with broken packaging. This can happen at any point in the supply chain. It can happen at the warehouse level when employees are manually stocking shelves or putting products away. It can also happen when a supplier ships items to the retailer.
Incorrect pricing and promotions
If the correct price is not attached to the correct product, this can lead to incorrectly priced products. It is also possible that a retailer will run incorrect promotions. This is especially true when retailers are manually updating their prices and promotions. The more manual processes that are involved in a company, the more likely it is that there will be an error in pricing or promotions.
Network integration issues
If systems are not integrated, it could lead to supply chain issues. For example, let’s say that a retailer is using a WMS (Warehouse Management System) to track items at the warehouse level. If the retailer is also using a different system to track sales, it could be easy to miss an order. Once it’s missed, it can be difficult to track down the order. This can lead to incorrect inventory levels at the store level and incorrect product assortment.
Conclusion
Supply chain issues can be costly to retailers and suppliers. They can lead to lost sales, unhappy customers, and frustrated employees. It’s important to work with a company that has expertise in supply chain management. This will allow companies to identify where there is a risk of supply chain problems and take steps to avoid them.